Ricoh 3D-Printing PPE Facial Shields
Joining HP Inc., Lexmark International, and several 3D-printer companies contributing to the production of personal protective equipment (PPE), Ricoh Europe announced on April 7th that Ricoh 3D is using its technology to produce 40,000 face shields a week for U.K. National Health Service (NHS) workers. Ricoh’s face shields are designed for better comfort and are said to be re-usable to reduce costs.
Based in Telford, U.K., Ricoh 3D is in discussions with medical establishments and NHS Trusts across the U.K., after working to get protective equipment to the frontline using the rapid prototyping capabilities of additive (3D printing) manufacturing.
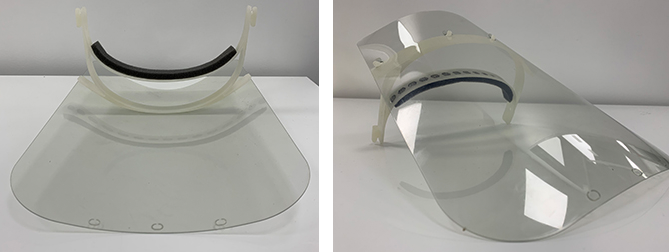
Just 24 hours after receiving the design file, the Ricoh team had the head support 3D-printed and remaining components sourced and assembled using its supplier network. Having refined the design to enhance comfort and reduce contamination, the face shield has now been approved for production.
Ricoh says that it’s estimated in London alone that more than 150,000 face guards will be used every day in the battle against COVID-19. It says it will upscale to full production using a 150-tonne injection moulding machine.
The company already produces over five million mouldings per month as part of Ricoh’s toner business, with capacity available at a moment’s notice at its 828m² injection moulding facility. Ricoh 3D has also had experience with various medical projects. These include development of a lever-hinge mechanism for ankle-foot orthotics and involvement in new technology with which limbs are scanned and precisely replicated using 3D printing prior to operation. Surgical instruments can also be produced using additive manufacturing and are typically used for intricate operations.
Mark Dickin, Additive Manufacturing & Moulding Specialist at Ricoh 3D, commented: “Our site is uniquely set up to take a product from concept to prototype to serial production, and that is exactly what we have done here in a very short timeframe. This really is a testimony to the strength of our supplier relations and the cross-functional team who made it happen so quickly.
“Local suppliers for the foam, elastic strapping and visor components have come forward across our production print, design solutions and quality assurance networks. We were seeing reports of nurses’ faces being cut and bruised by their existing protective equipment. Our frontline workers are battling enough already, without having to tend to sore and swollen faces at the end of a 12-hour shift. We knew our Polypropylene material was ideally suited for the job with its flexible, lightweight, watertight and fatigue resistant nature. Given its comparable properties to injection moulding, we had no doubts that this was the right material to support the transition to full moulded production.”
Jason Pott, Lead Research Nurse for Emergency Medicine at The Royal London Hospital, also commented: “In our tests, staff commented on the comfort of Ricoh’s solution over existing equipment. We tested across a range of male and female staff in the emergency department with different head shapes, hairstyles and head scarves – everyone was happy with the fit. Innovations like this help staff in the NHS to remain safe while caring for those in need.”
More Resources
- April 2020: Xerox to Mass-Produce Ventilators for COVID-19 Patients
- April 2020: Fujifilm Develops Faster COVID-19 Coronavirus Testing
- April 2020: Lexmark Producing Protective Face Shields for Area Hospitals
- March 2020: Fujifilm to Ramp-Up Production of Avigan to Fight COVID-19
- March 2020: HP CEO Enrique Lores Addresses COVID-19, HP Efforts